In today’s fast-paced industrial world, warehouses are crucial to the supply chain, but they can also be hazardous environments. One of the most frequent incidents reported is a “slip in a warehouse.” In fact, the New York Times (NYT) has highlighted various cases where workplace accidents have resulted in severe injuries and significant legal repercussions. This article will explore the causes, implications, and prevention strategies related to slips in warehouses, ensuring that employees can work in a safer environment.
The Significance of Safety in Warehouses
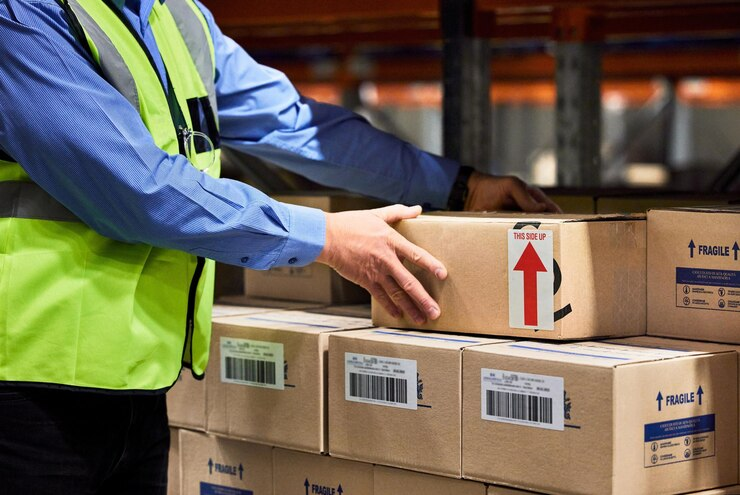
Warehouses, with their high traffic of forklifts, pallets, and human activity, are often fraught with risks. The NYT has addressed various aspects of workplace safety, emphasizing that employers must prioritize the well-being of their employees to maintain productivity and morale.
Common Causes of Slips in a Warehouse
Understanding the factors that contribute to slips in a warehouse is crucial for prevention. Here are some common causes:
- Wet Floors: Spills from products or moisture brought in from outside can create dangerously slippery surfaces.
- Uneven Surfaces: Cracks, holes, or irregularities in the flooring can cause tripping hazards.
- Cluttered Walkways: Materials, tools, or equipment left in walking paths can lead to accidents.
- Poor Lighting: Insufficient illumination can make it difficult to see potential hazards.
The Implications of a Slip in a Warehouse
The consequences of a slip in a warehouse can be severe. Injuries can range from minor sprains to serious trauma, which can lead to:
- Increased Medical Costs: Injured employees may require extensive medical treatment.
- Legal Ramifications: Employers may face lawsuits if found negligent in maintaining a safe workplace.
- Loss of Productivity: Injured employees may need time off work, disrupting operations.
- Reputational Damage: High-profile accidents reported by the NYT can tarnish a company’s reputation, leading to loss of business.
Legal Ramifications of Workplace Accidents
When a slip occurs in a warehouse, legal issues often follow. Employers have a duty of care to ensure a safe working environment. If an employee is injured due to negligence—such as failing to address a known hazard—the employer may be liable for damages.
Workers’ Compensation Claims
In many cases, injured employees may file workers’ compensation claims. These claims cover medical expenses and lost wages, but they can also lead to increased insurance premiums for the employer. According to the NYT, companies can face significant financial strain if they do not take proactive measures to enhance workplace safety.
Lawsuits for Negligence
In more severe cases, employees may choose to sue for negligence if they can demonstrate that the employer failed to maintain safe working conditions. This could result in substantial financial losses for the company and a long-term impact on its reputation.
Prevention Strategies for Slip in a Warehouse NYT
To mitigate the risks associated with slips in a warehouse, businesses must adopt a proactive approach. Here are some effective prevention strategies:
Regular Safety Inspections
Conducting routine inspections of the warehouse can help identify and rectify potential hazards. This should include:
- Floor Condition: Regularly check for cracks or wear.
- Lighting Levels: Ensure all areas are well-lit.
- Cleanliness: Maintain clear walkways and promptly clean spills.
Employee Training Programs
Educating employees about safety protocols is essential. Training should cover:
- Identifying Hazards: Employees should be able to recognize potential slip risks.
- Reporting Procedures: Encourage workers to report hazards immediately.
- Safe Practices: Teach employees the best practices for moving around the warehouse safely.
Effective Use of Signage
Prominent signage can alert employees to potential hazards. Signs indicating wet floors, uneven surfaces, or restricted areas can help increase awareness and caution.
Installation of Slip-Resistant Flooring
Investing in slip-resistant flooring materials can significantly reduce the risk of accidents. Options such as textured vinyl or rubberized surfaces provide better traction, especially in high-traffic areas.
The Role of Technology in Enhancing Safety
With advancements in technology, warehouses can leverage new tools to improve safety protocols. These technologies not only enhance safety but also streamline operations.
Automated Cleaning Systems
Implementing automated cleaning systems can help maintain floor cleanliness. These systems can quickly address spills and keep surfaces safe for employees.
Data Analytics for Risk Management
Using data analytics can help businesses track incidents and identify trends. Analyzing when and where slips occur allows employers to target specific areas for improvement.
Wearable Technology
Wearable technology, such as smart helmets or vests equipped with sensors, can monitor workers’ movements and alert them to potential slip hazards. This proactive approach can significantly reduce the likelihood of accidents.
Case Studies: Slip in a Warehouse NYT
Examining real-life incidents reported by the New York Times provides insight into the consequences of slips in warehouses and how organizations responded effectively.
Case Study 1: A Major Retail Distribution Center
In a prominent NYT article, a major retail distribution center faced multiple lawsuits after several employees slipped on wet floors due to improperly maintained cleaning schedules. The lack of immediate action led to severe injuries, significant financial loss, and a tarnished reputation. In response, the company overhauled its safety protocols, introduced mandatory training sessions, and invested in automated cleaning systems. As a result, they reported a 40% decrease in slip incidents in the following year.
Case Study 2: Innovative Flooring Solutions
Another NYT report highlighted a warehouse that successfully reduced slip incidents by investing in innovative flooring solutions. By installing specialized slip-resistant flooring and conducting regular safety audits, the facility saw a drastic reduction in slip-related injuries. Their proactive approach not only enhanced employee safety but also boosted overall productivity.
Best Practices for Employers
To foster a culture of safety, employers should adopt the following best practices:
Create a Safety Committee
Establishing a safety committee allows employees to participate in safety discussions. This fosters a sense of ownership and encourages everyone to contribute to creating a safer workplace.
Encourage Open Communication
Encourage employees to report safety concerns without fear of reprisal. Open lines of communication can lead to quicker resolutions and a more proactive safety culture.
Regularly Review Safety Protocols
Safety protocols should be reviewed and updated regularly to incorporate new technologies and respond to emerging hazards. This ensures that the safety measures in place are effective and current.
Conclusion: Prioritizing Safety to Prevent Slips in a Warehouse NYT
The risk of a slip in a warehouse is a serious concern for employers and employees alike. As highlighted in various reports by the New York Times, the implications of such incidents can be severe, leading to injuries, legal ramifications, and reputational damage.
More Read: